Building Blocks of Innovation: Spotlight on the Trailblazing PCB Manufacturers of Today
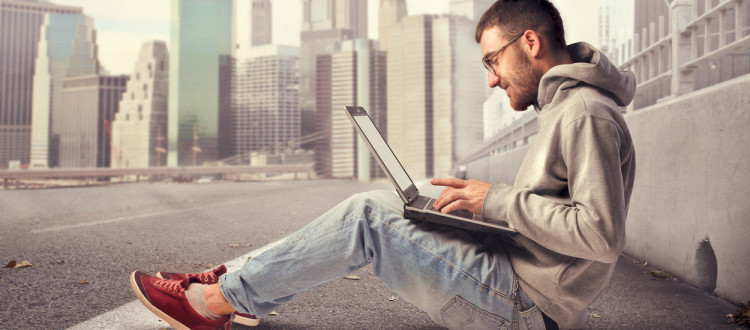
by John Edward by JOHN EDWARD
The coming age of manufacturing is nearer than you may realize. In truth, smart manufacturing is taking condition quickly because of improved agreement building across the vertical portions of the electronics manufacturing industry — printed circuit board assembly (PCBA) and semiconductors, outsourced semiconductor assembly and testing (OSAT). The merging of technologies, standards, and services across these vital sectors offers a valuable blueprint for smart manufacturing technology that the rest of manufacturing can emulate.
A report by Statista mentions that the worldwide market for smart manufacturing will hit $479 billion by 2023, pushed by the growth of smart factories and digital supply chains. The important developments in technologies will enhance manufacturing efficiency, safety, and productivity by incorporating real-time information analysis and synthetic intelligence (AI). Finally, customer experiences will improve because of increased connectivity, with better visibility and traceability of significant processes and results.
End-To-End Process – Thrust on Productivity and Cost Cutting
The electronics industry should take a comprehensive approach considering the entire process from raw materials to finished products. This involves understanding the front-end and back-end processes for making semiconductors, the creation of printed circuit boards, the assembly of electronic components onto circuit boards, and the production of final electronic systems. Such an integrated view helps companies identify opportunities to share enabling technologies and information across the semiconductor industry, companies that assemble and test semiconductor chips, and those that assemble printed circuit boards.
Faced with steep financial growth targets and declining margins, all industries are looking for ways to take advantage of smart manufacturing technologies to boost process and equipment reliability, productivity, capability, and cost savings. This drive to maximize profits is pushing companies across industries to adopt intelligent pcb manufacturing technologies that enhance the performance and efficiency of their operations from top to bottom. Additionally, the evolving nature of supply chains is resulting in significant changes to the traditional flow of materials through companies, further increasing the need for a digital system that connects all aspects of manufacturing from beginning to end.
Digital Building Blocks
Each segment within the electronics industry has reached different stages of sophistication regarding smart manufacturing. Advancements in semiconductors continue to outpace all others, continually creating demand for manufacturing processes that are smarter, more automated, and connected. However, there is little reason why other electronics industries like OSAT and PCBA cannot benefit from these innovations over time through sustained investment, even if they are lagging.
As diverse stakeholders participate in technology working teams and product prototype groups, can reach an agreement in an open, safe, and collaborative setting. Not only will this accelerate outcomes, but it will also provide a real-world viewpoint for analyzing expenses, risk profiles, and returns on investments. This method provides outstanding teamwork for other industry segments to model after.
The electronics industry can gain much from faster adoptions of IoT sensors, artificial intelligence, and machine learning. Growing chances exist to utilize digital replicas, which link the physical and digital realms with virtual representations of manufacturing processes, product designs, and system performance. Also crucial are building blocks that guide materials movement and changes, security, data examination, and interconnected solutions to enhance manufacturing machine management, process traceability, and factory-floor automation.
Evolution of smarter manufacturing
Projects based on practical applications from smart manufacturing will likely push the evolution of reference frameworks, organized data structures, and solid technologies to accelerate process optimization and incorporation. In the end, these initiatives will lay the groundwork for normalization and instructions for enhanced interoperability and interaction.
Final thoughts
In today’s world following the pandemic, it is sensible to expect more focus on connecting customers to what is happening on factory floors or in global innovation centres without requiring their physical presence. An emphasis on experience-based innovations will likely increase as it becomes clear that what happens within four walls must be extendable and visible to others, no matter where they or the facilities are located worldwide.
amazines.com
No Comment